Fluidline Valves
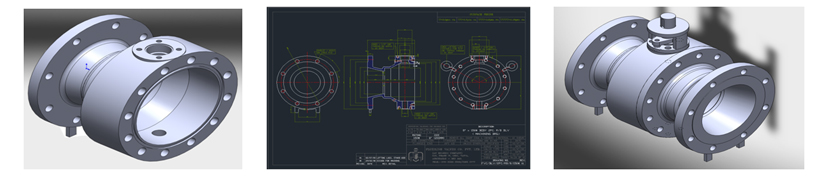
Oswal Industries Ltd
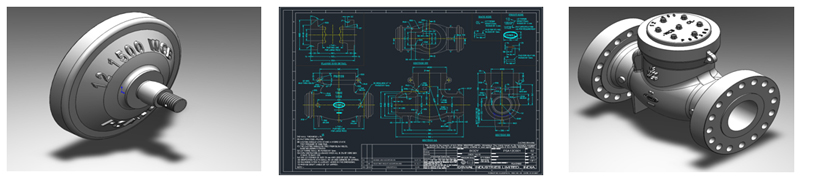
Hydro Mech
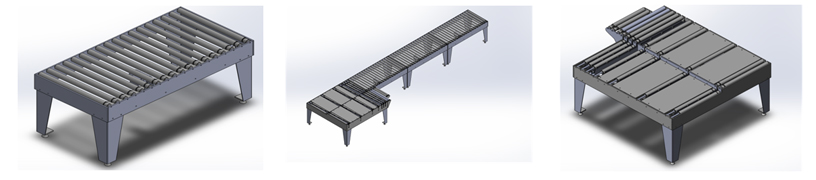
SKF Bearings
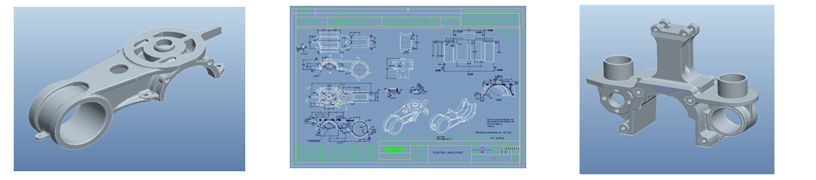
Scope
To optimize weight of existing crane without compromising its safety criteria.
Inputs
- 2D drawings along with material specifications
- Lifting loads
Challenges
Safety of Crane must not be compromised.
Outcome
Reduce weight of existing crane by 2000 kg
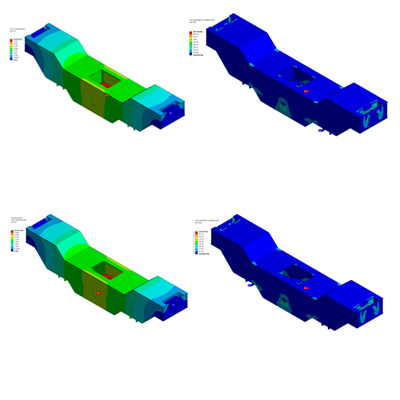
Scope
To Perform FE analysis for Solar Reflector Structure to check its stability against wind load acting in field.
Inputs
- 3D model with material specification
- Wind load
Challenges
If the Solar Reflector deflect more than allowable value than sun rays are deviate away from target. So deformation of Solar Reflector must be within in limits for its operating range against wind load for its maximum performance.
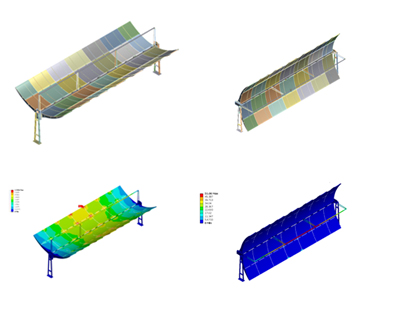
Scope
To optimize existing automatic casting machine structure.
New machine with high capacity is developed without making physical prototypes.
Inputs
- 2D Drawings
- Operating loads
Challenges
Existing Machine structures deflect more than allowable value while operating. These deflection must be within limits for its proper function as well as its operating life.
In development of new machine, loop holes in existing machine must be taken care of, to avoid unnecessary design trials.
Outcomes
With some modifications, design of existing machines is optimized.
Based on modifications in existing machine, new machine with high capacity is developed without making physical prototypes.
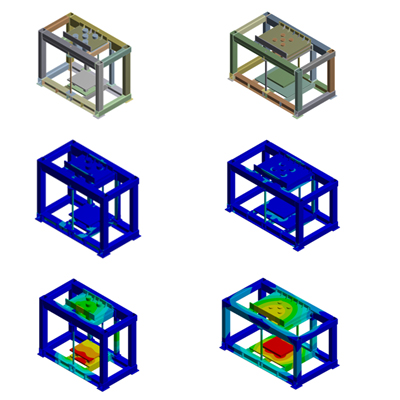
Scope
To perform Thermal-Structural analysis of rectangular type header box as per ASME, Section VIII- Div-2, Part-5.
Inputs
- 2D Drawings
- Operating loads, nozzle loads
Challenges
Code calculations are restricted due to complexity of geometry for given rectangular type header box with nozzle
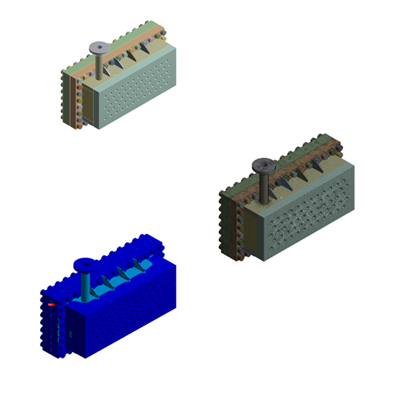
Scope
To perform Thermal-Structural analysis of part partition plate made of three different materials (for cost savings on materials) which are welded together by means of plug.
ASME, Section VIII- Div-2, Part-5 guide lines are used to perform analysis.
Suggest modifications to overcome failure due to operating loads.
Inputs
- 2D Drawings
- Operating loads, nozzle loads, Differential pressure acting across PP plate
Challenges
As PP (Part Partition) plate is consist of three different plates, these three plates have different thermal expansion coefficients at operating temperature. Also these plates are welded together by the means of plug welding. So, these plates deforms in different manner at operating temperature.
Outcome
Stiffeners are added at suitable locations in existing design to overcome failure.
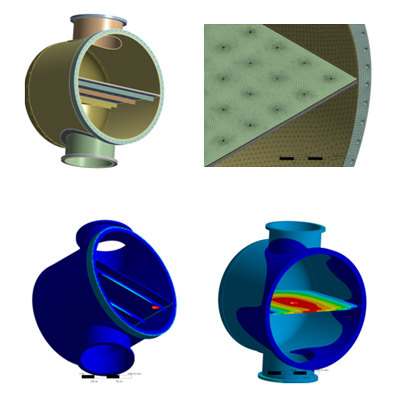
Scope
To perform Structural analysis of Jacketed nozzle to check its stability against loads as per ASME, Section VIII- Div-2, Part-5.
Inputs
- 2D Drawings
- Operating loads, nozzle loads
Challenges
Code calculations are restricted due to complexity of geometry of Jacketed nozzle.
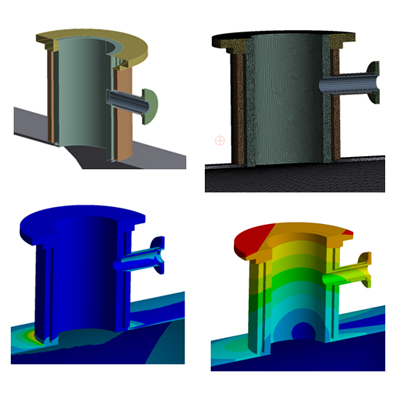
Scope
To perform Structural analysis of fixed type tube sheet to check its stability against load acting on it due to differential thermal expansion of shell and tubes in a heat exchanger.
Inputs
- 2D Drawings
- Design loads & temperature
Challenges
Code calculations are restricted due to complexity of geometry of given tube sheet. As per code knuckle radius of tube sheet should be minimum 3 times of thickness but due to design constrains, this radius is kept below the allowable values.
Tube bundle must be include in model to consider its stiffness effect on tube sheet.
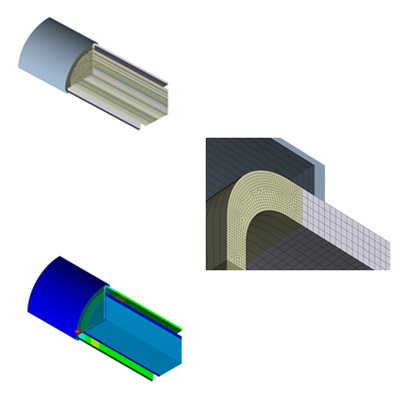
Scope
To perform CFD analysis of air cooled heat exchanger to analyze flow pattern, temperature distribution and pressure drop of water as well as air.
Inputs
- 2D drawings
- Temperature, Mass flow rate and fluid pressure
Challenges
Multiphase analysis is performed. Conjugated heat transfer model must be considered.
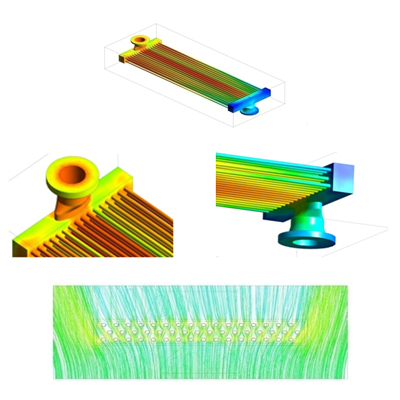
Scope
To perform CFD analysis of automobile radiator inlet header to analyze flow pattern and pressure drop of cooling water.
Inputs
- 2D drawings
- Mass flow rate and fluid pressure
Challenges
Existing radiator design has to be modified for uniform mass flow rate in tubes and reduce pressure drop at the inlet header.
Outcomes
With modified design uniform flow rate in tubes was achieved with optimized pressure drop across the header.

Scope
To perform CFD analysis of multiport selection valve (MSV) & analyze its flow capacity.
Inputs
- 2D drawings
- Mass flow rate and fluid pressure
Challenges
Due to physical dimensional limitations of valve, physical testing is not possible. Flow capacity in other words flow co-efficient plays an important role in design and selection of valves.
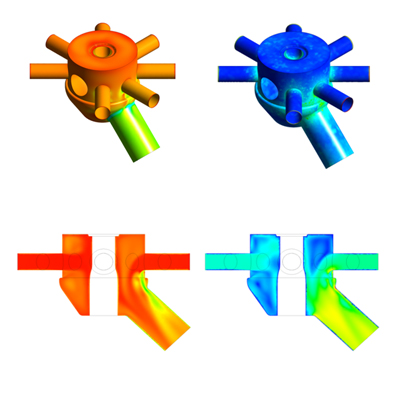
Scope
To develop a pump based on fundamental parameters like head, flow rate and RPM.
Inputs
- Head, flow rate and RPM
Challenges
Existing pump with same parameters have efficiency lower than required.
In addition to improved efficiency, client needed the same design to work at different design points with little compromise in efficiency by trimming the impeller diameter.
Outcomes
With the new design, overall efficiency was improved by 10 % with weight reduction of 8 %. This design shall work at other 4 design points by trimming the impeller diameter.
So, overall cost savings is achieved in energy, material, die and pattern.
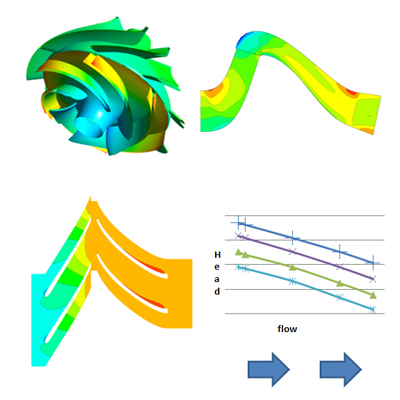